Tooling Group Leader
Not SpecifiedBookmark Details
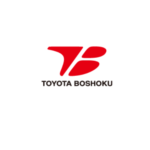
Toyota Boshoku America
I. General Summary:
I. Directs Team Leaders and other Team Members in tooling machine room activities and in the execution of the group’s responsibilities. Support the manufacturing areas with plant focus on minimizing down time, increasing productivity and maintain the overall Toyota Production System as well as company policies/procedures. As a tool and die machining department group leader, you will lead your team to make & repair details to maintain progressive and transfer stamping tools. This position is excellent for a Tool & Die Maker with exceptional technical expertise and a positive, team-oriented attitude looking to work for a company where they can grow and hone their own and other TMs skills. You will manage your team as an operational unit and will be responsible to accomplish company goals and targets in accordance with all company policies, maintenance standards and methods, and standards for safety, quality, productivity, cost reduction, housekeeping, efficiency, training, teamwork, and morale.
II. Primary Responsibilities/Essential Job Functions:
• Function as a first-line supervisor over team leaders and team members of the T&D machining department.
• Plan and coordinate hiring and placement of team members with his/her Assistant Manager. Monitor and track staffing conditions, work hours and overtime, job rotation, and absenteeism of the T&D machining department.
• Understand, execute, and ensure consistent compliance with all company rules, policies, and practices, and take appropriate corrective action when warranted, in accordance with the terms of the TBA policies.
• Responsible for managing and appraising team member job performance and administrating coaching and corrective action as needed.
• Develop and maintain positive team member relations centered on mutual trust, dignity, respect, fairness, consistency, two-way communication, teamwork, and harmony.
• Provide direction and motivation to team members emphasizing safety, quality, efficiency, productivity, cost reduction, and morale.
• Utilize Toyota Production System (TPS) techniques to standardize current/new processes and methods, reduce process variation, identify waste, and methodically eliminate waste.
• Develop standardized work procedures by designing and/or documenting the best work sequence for each piece of equipment and/or die details.
• Direct the work of Team Leaders and Team Members by assigning/re-assigning work stationing based on current work situation and production schedules.
• Perform the essential job functions of team leaders or team members as necessary to maintain efficient, stable, and continuous operations in the T&D machining department.
• Monitor the flow of parts, materials, productivity, and quality with respect to machine, equipment, and tooling operation; take corrective action as needed.
• Act as a technical problem solving resource in the T&D machining department by determining the root cause and countermeasure required, especially in the case of equipment-related manufacturing interruptions.
• Troubleshoot daily safety, machine, equipment, and tooling issues.
• Will work with equipment technicians to ensure equipment issues are resolved in a timely manner.
• Be proactive in predicting abnormalities and finding innovative solutions to correct.
• Lead continuous improvement activity for the T&D machining department.
• Participate in the setting of Key Performance Indicator (KPI) targets for the T&D machining department as a method of continuous improvement.
• Maintain, monitor, and update department and KPI board and graphs, daily, and initiate continuous improvement activities in the T&D machining department.
• Ensure compliance with safety regulations, PPE requirements, and company safety policies and procedures.
• Lead, perform, and/or participate in 5S housekeeping, accident investigation, and safety audits and related activities.
• Maintain knowledge of procedures concerning Hazardous Waste, Spill Response, and Plant Security.
• Train and coach team members to maintain productivity and quality standards, environmental, safety, quality, job performance, setups, trouble shooting, continuous improvement, and maintenance and repair operations in the T&D machining department. This will include new team member training and cross training as needed.
• Maintain training matrix for team leaders and/or team members, assuring training is effective and corrects substandard performance in the T&D machining department.
• Maintain, plan, and prepare department instruction manuals.
• Ensure further development of team members through performance evaluation, development of training plans, feedback, coaching, and cascade training.
• Collect, record, and analyze information while maintaining documentation regarding the activities in the T&D machining department as defined by company policy, procedure, or practice.
• Prepare business reports and spread sheets of required data.
• Maintain specified records, files and logs of department/shift activities such as equipment problems, utility operations, maintenance, repair, etc. (manual and computer) as required. Perform other various administrative duties.
• You will hold daily communication meetings, keep team members informed on issues relevant to them and encourage two-way communication.
• Maintain daily and/or frequent communication with upstream and downstream groups/areas and support departments to ensure efficient and stable operations in a team-based environment.
• Coordinate communications between shifts in the T&D machining department.
• Daily use of Asset Essential to make work orders / complete work orders/ to track you and your teams work.
• Must work daily with the other TBTN T&D GL /TL to complete the required task to ensure production can run as needed.
• Use precision measuring instruments like calipers, micrometers, height gauge, to check the tool’s dimensions to insure accurate part quality.
• Work with the Engineering department to improve TBTN dies and other processes as needed.
• Other duties as assigned.
III. Minimum Qualifications/Requirements:
Education:
• High School diploma or equivalent required.
• Machinist 1 certificate/diploma or equivalent required.
• Tool and Die certificate/diploma or equivalent experience a required.
Experience:
• Previous Leadership experience in a T&D environment required.
• 2 years’ experience programming setting up CNC machines required.
• 2 years’ experience useing in Mastercam /Solid works/ or Autocad required.
• 2 years’ Tool & Die Progressive die experience required.
• 2 years’ experience in drawing in Mastercam/Solid works / or Autocad preferred.
• Automotive industry experience preferred.
• Working knowledge and experience with the Toyota Production System preferred.
Personal/Technical Skills:
• Good leadership and communication skills a must
• Ability to lead a team of technical skilled tool & die technicians
• Ability and Willingness to participate in additional training as needed and identified by the Tool Room Supervision.
• Good problem solving and analytical skills.
• Flexibility in a changing working environment.
• Good math and communication skills.
• Experience with precision measuring equipment.
• Strong attention to detail.
• Strong customer service orientation.
• Ability to consistently show and maintain professionalism.
• Highly motivated, ambitious self-starter.
• Ability to work in a fast-paced, multicultural work environment.
• Ability to communicate and work well with all levels of the organization, and with multiple departments.
• Ability to complete forms and reports, including the ability to read, write, and follow detailed instructions.
• Ability to exercise on daily basis.
• Ability to use diverse hand tools and equipment.
• Ability to be adaptable and flexible in a constantly changing environment.
• Be able to maintain the confidentiality of any information encountered.
• Ability to read and interpret blue prints, schematics, drawings, specifications, and technical instruction manuals.
• Thorough understanding of company product, trade terminology, maintenance and repair operations, manufacturing processes, and machine/equipment operation.
Language Skills:
• Any combination of the following skills is a plus
o English written and verbal
o Japanese written and verbal
o Spanish written and verbal
Computer/Software:
• Basic Microsoft Office applications required
• 2 years of cam experience required
• Ability to use Asset Essentials required
IV. Work Environment/Conditions:
Plant:
Standard automotive plant environment with high decibel noise levels, flashing lights, and alarms/notification systems. PPE (Personal Protective Equipment) such as safety glasses, safety toe shoes, hearing protection, etc. may be required in engineering, manufacturing, or industrial areas. Personal attire standards may apply.
TBTN- temperature controlled environment
Team Members are exposed to sharp metal objects that are heated during welding process. As such, Team Members are required to wear heat protective gloves and sleeves that are made from an XKS nylon material. The PPE is designed to cover all of arms and hands and can become hot during summer months.
II. Physical Demands:
Capable of standing 100% of time and must be able bend, walk, & to lift up to 30 pounds.
While performing the duties of this job, the team member is frequently required to grip tools and objects, stretch and/or reach with hands and arms; using hands to finger, handle, feel, twist, walk, twisting (standing), bend at the waist, and do repetitive motions. The team member must occasionally kneel, work from heights and crouch. The team member must frequently lift and/or move five to fifteen pounds. The team member must regularly lift twenty to thirty pounds and occasionally lift and/or move over thirty pounds with the assistance of a cart, pallet jack, other mechanical device or another team member. While performing the duties of this job, the team member is required to talk, see, and hear.
Disclaimer: This job description is intended to identify the general nature and level of work performed by team members within this classification, as well as certain essential job functions. It is not intended, and should not be interpreted, as a comprehensive inventory of all duties, responsibilities, and qualifications required of team members assigned to this job. To qualify for this job, however, a team member must be able to perform its essential functions with or without reasonable accommodation. Under no circumstances may this job description be construed as altering the at-will nature of the employment relationship between TBA and any team member.
Share
Facebook
X
LinkedIn
Telegram
Tumblr
Whatsapp
VK
Bluesky
Threads
Mail